Companies
Tailwater: Removing Nitrates Affordably
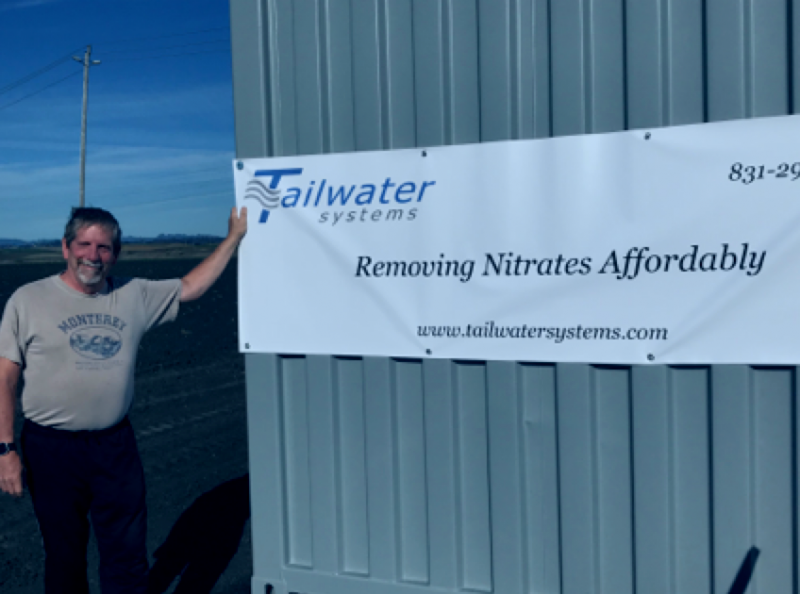
By John Skardon
Founder of Tailwater Systems
Special to Santa Cruz Tech Beat
July 17, 2018 — Santa Cruz, CA
(Photo above: John Skardon is the founder of Tailwater Systems. Contributed.)
“One of the most exciting applications for our denitrification process is drinking water — specifically nitrate contaminated wells in small communities.”
My wife Mariko and I returned to Monterey Bay in 2011 after years in the corporate world. I began teaching locally at two universities. I was asked by a colleague early in 2014 to assist in a project related to “nitrate removal” using woodchip bioreactors. These bioreactors were long trenches, about 4-6 feet deep filled with woodchips. The bioreactors were then covered with liner and overburden. Surface runoff from agricultural fields would be pumped into one end of the trench. Twenty four to forty eight hours later, the waste water, now denitrified, would exit the reactor and return to the waste stream. Inside the reactor, denitrifying bacteria would attach to the wood chips, consuming the nitrate from the water and slowly dissolving the woodchip as a carbon substrate source. The nitrate would be converted to nitrogen gas via a series of enzymatic reactions by the bacteria consortia.
Typical removal rates or efficiencies for these reactors were in the range of 10-50 grams of nitrate removed per day, per cubic meter of wood chips. It did not take a genius to realize that a 190 liter/minute wastewater flow rate with 0.1 grams/L concentration of nitrate would require an enormous volume of wood chips. Local growers and property owners made it very clear to me in the early stages that they were not going to dig up productive land and create an in-ground wood chip bioreactor.
I begin reverse engineering this problem and started with the wood chips. Part of the solution was to replace the wood chips with a much more effective biofilm support. Wood chips normally have a specific surface area (surface area/volume) of 1.5:1 to 2:1. Modern biofilm carriers, developed early in the 1990’s had specific surface area values of > 400. Clearly, if we could substitute these plastic carriers for the wood chips, we should get a huge improvement in the rate of denitrification.
Next I looked at the configuration. A horizontal flow reactor only makes sense in liquid-gas reactions if you can maintain an extremely uniform flow. But all of the other biological “filters” in use for this application were all vertical flow systems. This is the point where I got really excited — why not build a vertical, plug flow reactor using just plastic water tanks and these carriers? This solved several problems. Vertical flow would enable very uniform nitrate removal and dramatically reduce the physical footprint. The biofilm carriers would give us a huge increase in the amount of denitrifying bacteria. The systems would be above ground, enabling easy setup, and easy relocation by the grower or property owner if needed.
There were three remaining hurdles: a) isolating a suitable consortia of denitrifying bacteria, b) developed a control and monitoring system and strategy, and c) identifying which carbon substrate should be used to feed the bacteria. I developed a very simple and repeatable technique for isolating the bacteria. The control system was pretty easy- just use what the big utilities were using. Finally, I was able to locate and test a very concentrated substrate, currently produced in high volumes in the US. This substrate met my requirements for cost and safety.
In early 2017, A local grower and property owner gave me space to build and operate my first prototype bioreactor. My wife and I used our own funds to get started. With help from former student Hunter Burnham, we put together the first bioreactor in about 4 hours. Within 14 days, we were reducing the nitrate levels from 70 mg/L to less than 10 mg/L in just under 90 minutes at 2 gallons per minute. The denitrification rate was impressive — consistently at 1500 grams per cubic meter, per day.
We are now installing production bioreactors in the central coast area. Our timing for our denitrification business may be good as many regulatory pressures are forcing local growers and property owners to remove nitrate from groundwater and surface runoff. Our first patents have been filed and we are optimistic about the future.
One of the most exciting applications for our denitrification process is drinking water — specifically nitrate contaminated wells in small communities. Hundreds if not thousands of wells in California are contaminated with nitrate. Desperate communities are left with buying drinking water or digging a new well. But new wells are much deeper and the pumping costs increase dramatically. After working with regional and State drink water engineers we found that we should be able to “turn on” these shallow wells by using a hybrid drinking water system. Reverse osmosis would be used to produce the drinking water and our denitrification system would be used to remove nitrate from the RO waste or concentrate. The denitrified concentrate can be disposed locally. This solution does not required any special permitting.
###
Learn more at http://www.tailwatersystems.com
###
Tagged John Skardon, Tailwater